Home » Technical development » Blown film production
Blown film production
The blown technology is the most common and preferred production method for films. Equipment used for this manufacturing method are capable to produce films with a thickness tolerance of ±15–20%. In practice, this assumption covers a film with its thickness fluctuating between 16 and 24 microns. According to the "weakest link" analogy, the general strength of this film is not higher than at its weakest point. In other words, it does not offer more than a film with a thickness of 16 microns exactly. Driven by this problematic endowment, a new technology with a more precise production capability, that could eliminate the significant amount of unnecessary material surplus in the finished product while remaining at the same level of strength, have begun to outline (see Figure 1).
The above criteria formed the basis for the development of a manufacturing process. Nevertheless, when the team of engineers completed their efforts, they have possessed a new technology capable for producing PE film with not only a thickness tolerance of ±–2 but also with an advanced structure. This structure has a mesh arrangement with a better orientation that results in increased mechanical parameters by 10–15%.
With the thickness-controlling capability of this new technology, a nominally 20-micron thick film could be replaced by a 17.5 micron thick one. Taking the second advantage into consideration will lead to a perfect replacement by even a 16 micron thick film. This achievement allows an approximately 25–30% material economy that may end up in reducing the environmental strain by several million tons internationally.
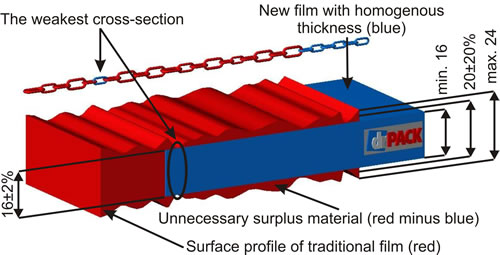
Figure 1. Cross section of a film
The development of the blown manufacturing technology was supported by the team's year-long research experience. The aim and result of the development was therefore an equipment that produces film at high speed with even thickness and material quality, better failure strain and advanced elongation parameters. The two fundamental novelties of this equipment is the die with a rotating core that shapes the bubble, and the intensive air-cooling system performing the fast recooling of the bubble.
The cardinal differences between the traditional rotating die and the die with a rotating core, that legitimate the manufacture of the newest generation of films, is described below.
The production of a perfect film assumes that the material leaving the nozzle's constant-size slit and entering into an intensively and evenly cooled space is homogeneous in all parameters (thickness, temperature, structure, circumferential speed etc.)